Changxing Island, located near Shanghai, stands as a beacon of China's shipbuilding prowess, housing the nation’s largest and most advanced shipyards.
China has dominated the global shipbuilding market for 14 consecutive years. It has three major shipbuilders: Jiangnan Shipyard, Hudong-Zhonghua Shipbuilding, and Shanghai Waigaoqiao Shipbuilding. All of them rank among the world's top ten in terms of order volume.
Situated 40 kilometers from downtown Shanghai, Changxing Island boasts a sprawling 14-square-kilometer factory space along a 16-kilometer-long deep-water shoreline. Over 70,000 people are work in the docks and on the piers, with the number of ships under construction once surpassing a record high of 60.
On Changxing Island, the most cutting-edge vessels at Jiangnan Shipyard include dual-fuel container ships, which can reduce greenhouse gas emissions by 28 percent per voyage; China's fifth-generation LNG carriers, with a 174,000 cubic meter capacity to supply gas for a month to 3 million households; and the world's largest new-generation ultra-large container ship, capable of carrying 24,000 containers.
"The current task involves cutting the plates for the middle section of the ship’s deck. With our machinery, we can process about 15 full plates in an 8-hour shift," said Li Jiajia, an engineer from Jiangnan Shipyard's manufacturing department.
The shipyard’s plasma cutting machines enable automatic cutting with exceptional precision and high speed, capable of slicing through 50-millimeter-thick steel plates in seconds. However, shaping these thick plates into curved forms remains a challenge.
In the cold press workshop, a domestically developed three-dimensional computer numerical control (CNC) bending machine with over 100 independent press heads has dramatically boosted efficiency through hydraulic and servo motor control.
"We can increase efficiency by five to ten times. Now our operators work in computer rooms, with improved working environment and incomes," said Wu Yizhong, an operator at Jiangnan Shipyard.
During the shipbuilding process, sections of steel plates are welded into segmented components of the ship's hull, then transported to the dock for final assembly, facilitated by comprehensive digitalization of shipbuilding.
In the virtual reality (VR) interactive training room, equipped with four walls of screens, engineers use a digital platform and headsets to simulate and improve the ship's internal structure, reducing errors.
"On the model, we can pinpoint issues reported from the site, allowing for more precise coordination. This showcases the transformative impact of digitalization," said Wang Jie, a digital design supervisor at Jiangnan Shipyard.
Moored at the pier is a liquefied natural gas (LNG) carrier, renowned globally for its advanced technology, high added value, and reliability. Hudong-Zhonghua Shipbuilding now holds orders for over 50 carriers scheduled for production until 2031.
Building an LNG ship involves the installation of invar steel, which is used to insulate liquefied natural gas. Despite being as thin as two layers of eggshell, invar steel can maintain its shape from 20 degrees Celsius down to minus 163 degrees Celsius.
This advanced steel, developed through collaboration between Hudong-Zhonghua and upstream enterprises, effectively replaces imported materials.
"The performance metrics of our vessels are already leading globally. The future prospects for shipbuilding are very promising, and I am confident," said Huang Huabing, deputy chief engineer of LNG at Hudong-Zhonghua.
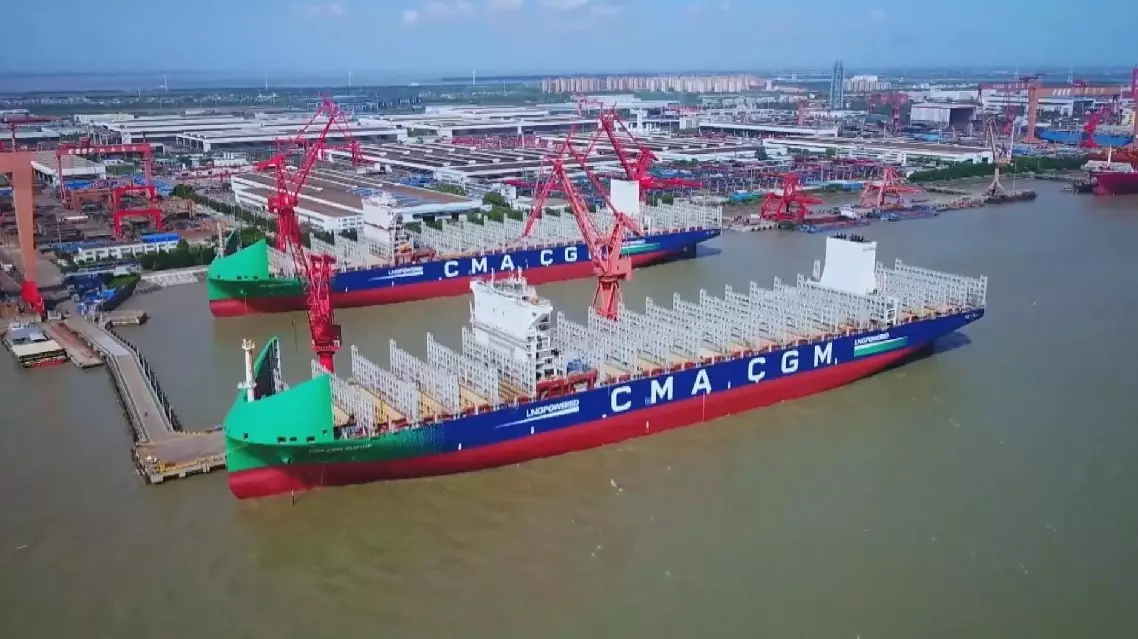
Shanghai's Changxing Island leads China's shipbuilding innovation