Through intense cross-sectoral cooperation, north China's Shanxi Province has further processed industrial pollutions by turning them into useful products and clean energy.
The Jinnan Steel Group in Shanxi's Linfen City needs to use 7,500 tons of coke and 19,000 tone of melted iron to produce 24,000 tons of steel every day. In this process, 2.76 million cubic meters of converter gas will be generated.
While for a local coking factory, it will produce more than 9,000 tons of coke every day, along with 3.78 million cubic meters of coke oven gas.
Since these waste gases cannot be emitted directly, then how to deal with them?
"Traditionally, we would heat up and burn the coke oven gas to generate electricity. This is highly energy-consuming with massive emissions. Now, we'll send the extra coke oven gas to chemical plant," said Shi Yunpeng, director of Jinnan Steel Group's Liheng coking factory.
In the chemical plant, these waste gases were changed into useful products, such as glycol and liquefied natural gas.
"After chemical process treatment such as compression, purification, separation and purification, coke oven gas and converter gas will turn into 300,000 tons of ethylene glycol and 150,000 tons of liquefied natural gas products per year. Such treatment will also reduce 1.36 million tons of carbon dioxide emissions from the upstream industry," said Han Tingjie, chief despatcher of production technology department with Shanxi Woneng Chemical Technology Co., Ltd.
The pollution can also become hydrogen, which will later replace coke to heat up blast furnaces for making iron.
"After hydrogen smelting, this blast furnace can cut coke by 40,000 tons per year. So three blast furnaces can reduce 120,000 tons of coke and 330,000 tons of carbon dioxide emissions every year," said Ding Chao, person in charge of Jinnan iron mill's No.3 blast furnace.
For now, Shanxi's steel and coking industries have said goodbye to high pollution and high energy consumption, heading towards an environment-friendly future.
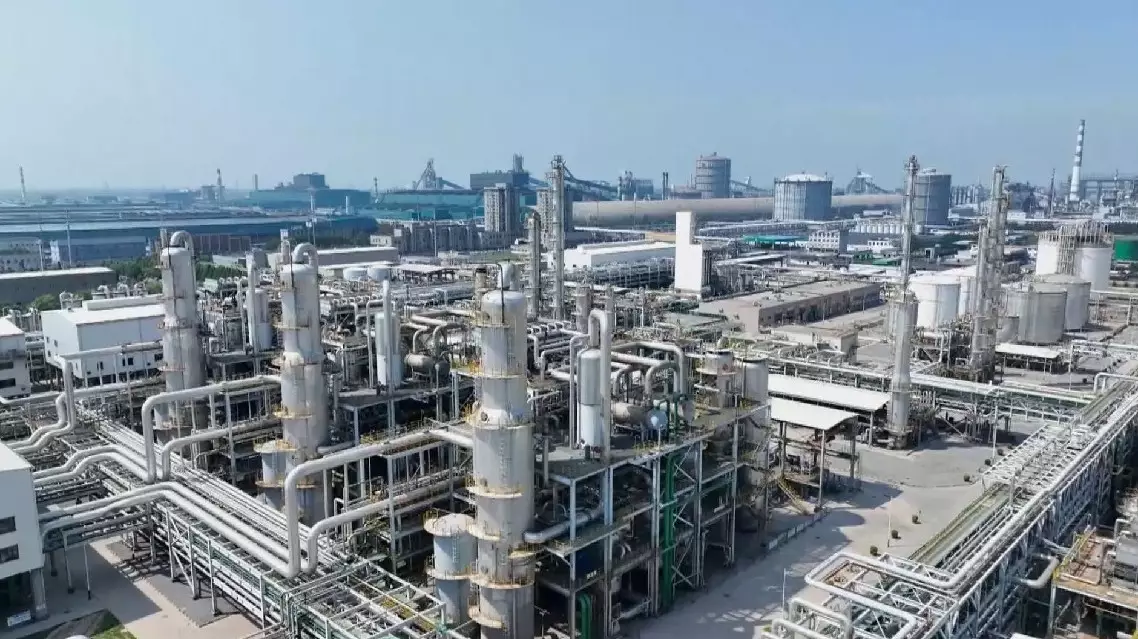
Coal-rich Shanxi Province steps up environment-friendly low-carbon circular growth