A Sino-Italian joint venture in north China has been committed to manufacturing high-quality products for high-speed trains by depending on its strict production techniques and made efforts in building a research and development team to realize the transformation from technology import to technological innovation, giving a boost to the rapid development of China's high-speed rail industry.
Zhiqi Railway Equipment Co., Ltd., established in 2007 in Taiyuan City of Shanxi Province, now boasts the independent production capacity of high-speed rail wheelsets, and contributes to the safety and stability of high-speed rail trains through strict processing technology and comprehensive performance testing.
Only four wheelsets, consisting of wheels and axles, are needed to support a carriage of the "Fuxing" high-speed train weighing about 60 tons.
The whole production process of wheelsets mainly refers to eight strict and precise procedures such as rough processing, fine processing, testing and flaw detection.
So far, the company has an annual production capacity of 50,000 wheelsets, with products used in mainstream train models including "Hexie," or harmony, and "Fuxing," or rejuvenation.
"The requirements for processing technology of high-speed rail wheels are very precise and strict. We need to control the processing error of the wheel size within 0.02mm, which is about one third of the human hair's width, and the quality inspectors need to control the measurement error within 0.005mm, about one twelfth of the hair, so as to ensure the safe operation of high-speed trains," said Liu Hao, an engineer.
In addition, the manufacturer also undertakes the tasks of product research and development and testing.
During the period of more than a decade since its establishment, the company has set up a professional independent design and development team for high-speed EMU wheels and axles, and has also built a systematic and rigorous laboratory that can carry out a full range of performance testing and evaluation of products in line with different standard systems in countries and regions like China, Europe, North America, and Russia.
"The eccentric motor repeatedly applies eccentric force to the axle to make it shake, simulating its actual operation. So far, this test has been carried out 420 million cycles, simulating the situation that axle has run 1.26 million kilometers. After the test simulates the situation of axle running 1.65 million kilometers, we will start to study the law of crack growth," said Cui Yuxuan, a researcher.
Relying on the deep exchange with Italy, the two sides of the joint venture have learned from each other in design, technology and testing, and successfully completed the goal of technology introduction and innovation over the past couple of years.
"In the future, our company will continue to give full play to our unique technological and production capacity advantages, and continue to carry out in-depth cooperation with foreign partners around the intellectualization, lightweight and environmental protection of products, so as to provide more reliable products and better services," said Huo Fengfeng, chief engineer of the company.
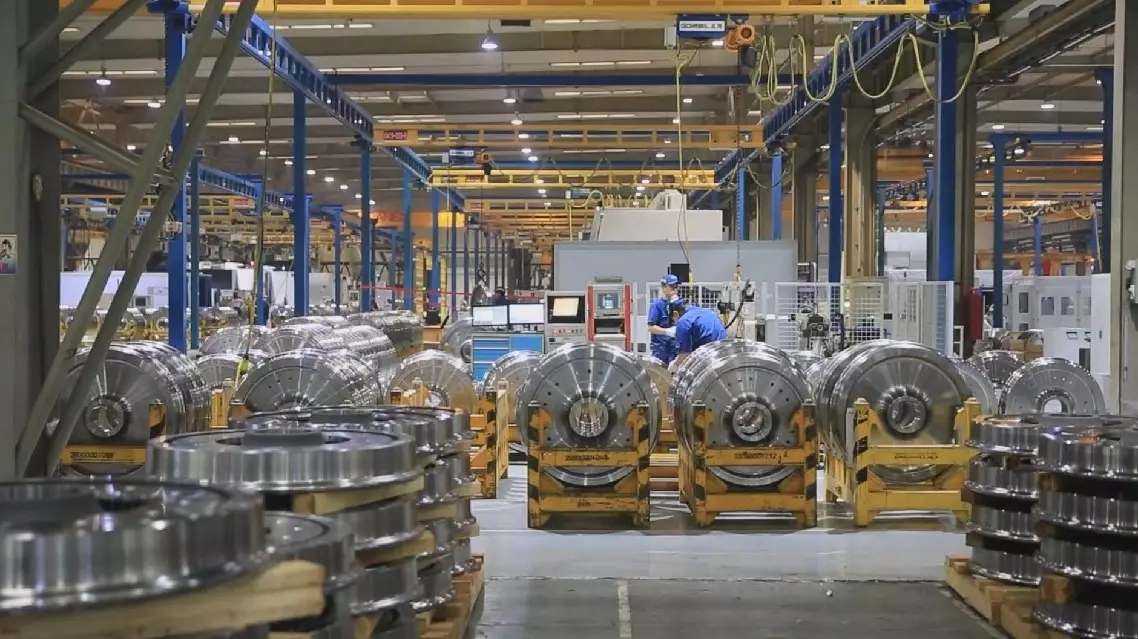
Sino-Italian joint venture dedicated to enhancing operation on high-speed trains