A steel plant in east China's Shandong Province has greatly improved its production efficiency and enhanced the first pass yield of its industrial steel to over 99.997 percent with the help of an intelligent monitoring and control system.
The plant, owned by Shandong Iron and Steel Group Yongfeng Lingang Corporation in Linyi City, is equipped with more than 30,000 sensors that can collect over 1 million data points from the entire factory.
Through 5G technology, 741 pieces of information are transmitted to the intelligent control center every second and then displayed on the large screens there.
Based on the operating data, more than 40 staff members at the control center would make instructions to the system to adjust operations of the production equipment.
"The system mainly collects data about equipment operation status, voltage, current and vibration spectrum. It has so far successfully predicted more than 100 production equipment failures," said Zhang Kai, director of equipment office of the company.
When the system detects abnormal situations on the production line, such as cases where the power consumption is approaching the ceiling, it would alarm the staff at the control center.
"In the past, we dispatchers have to make at least a dozen of calls to solve such a problem. Now, we just have to make one call, and the power load would be reduced in five minutes," said Hou Qinghai, a power system dispatcher.
"This is the multifunctional sensor on our rolling line. Like the five basic human senses, it can monitor various production conditions on our entire rolling line in real time, raising our response efficiency to abnormal situations by over 50 percent," said Fu Ruide, a workshop supervisor of the company.
The intelligent system can also help the plant reduce carbon dioxide emission by over 800,000 tons per year.
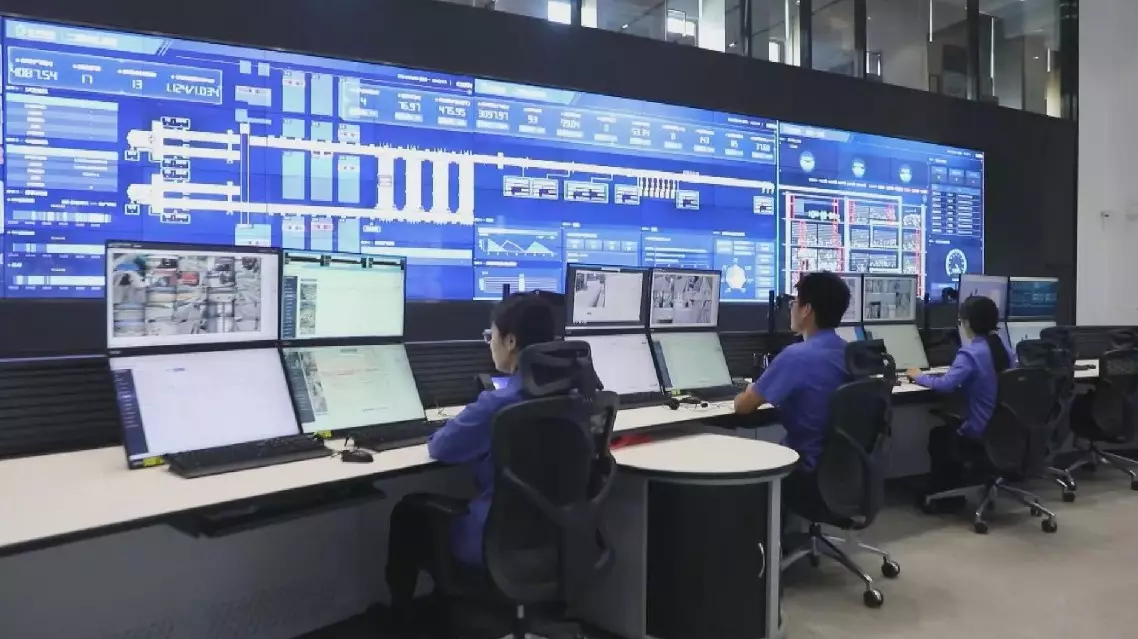
Intelligent transformation helps east China steel mill improve efficiency