The production of China's independently developed AG600 large amphibious firefighting aircraft is progressing smoothly as the aircraft on Sunday obtained its type certificate from the Civil Aviation Administration of China (CAAC) in Beijing.
The certificate acquisition marks the successful development of AG600 and its approval to enter the market.
Located in Jinwan District of southern coastal city of Zhuhai, the birthplace of AG600 is the only special large aircraft production line in China that is open to the public.
The general assembly line of AG600 also serves as a national patriotism education demonstration base, with three exhibition areas of aviation culture, assembly production, and science popularization and research.
"The entire final assembly production line of the AG600 aircraft consists of six stations. When we say 'station,' we actually mean the workstation where the aircraft is being assembled. The station we are currently at is what we call Station 51, which is the major fuselage assembly station. The main task here is to join the forward fuselage, the center fuselage, the aft fuselage, as well as the wings and the vertical and horizontal stabilizers. The primary structural work is completed here and we can also describe it as building the entire skeleton of the aircraft. The station we see now is called Station 41, which is the system installation and debugging station. If we compare the aircraft to the human body, then Station 51 is like building the skeleton, while Station 41 is equivalent to installing the blood vessels and nervous systems," said Ma Jianming, head of AG600 general assembly line of South China Aircraft Industry Co., Ltd under China Aviation Industry General Aircraft (CAIGA).
Apart from the Station 51 and 41, the factory also has Station 52 for fuselage prefabrication, Station 53 for left and right outer wing automated docking, Station 54 for vertical tail docking, and Station 31 for full aircraft joint debugging and testing, according to Ma.
The entire factory operates as a station-based pulse production line, built on principles of digitalization, informatization, modularization, and flexibility. It features a fully automated docking and posture measurement system. According to Ma, the production line is capable of assembling over 10 AG600 aircrafts per year, with capacity that can be scaled up at any time based on demand.
"When the aircraft moves from one station to the next, it follows a fixed rhythm, for example, shifting forward once every 50 days. In this way, we can vividly see that it 'pulses' with each movement. Essentially, a pulse production line means that the aircraft progresses through the line at a steady and predetermined pace," he said.
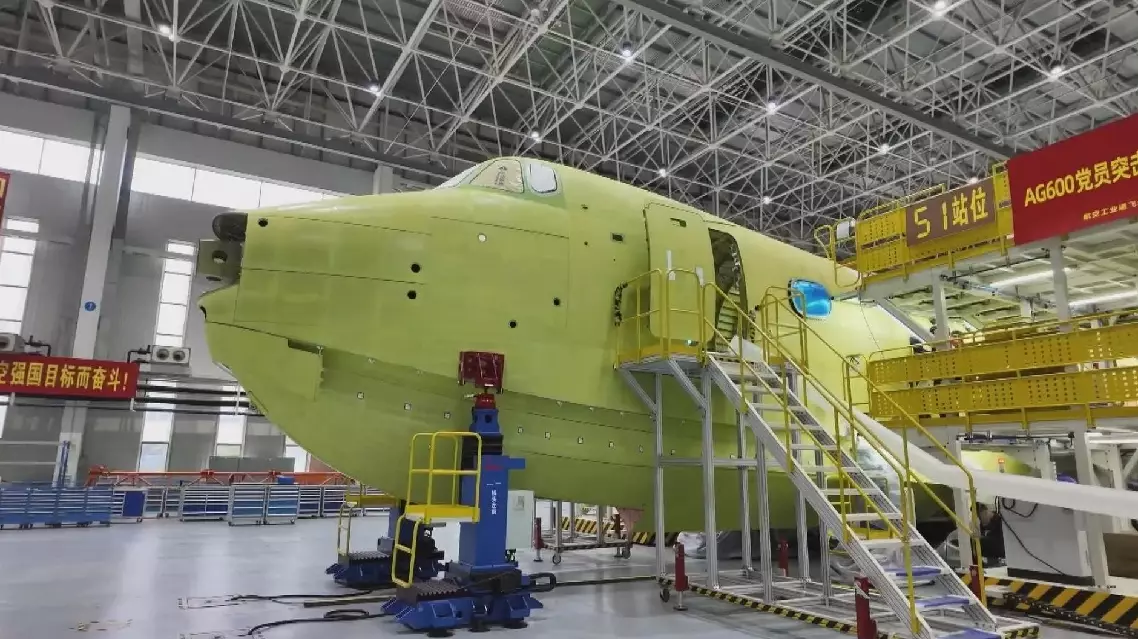
China's AG600 amphibious aircraft production progresses smoothly following certification