China claimed most spots in the latest batch of global "lighthouse" manufacturers issued by the World Economic Forum (WEF), showing the country's significant progress in the green and high-tech transformation of its manufacturing sector.
The WEF, along with consulting firm McKinsey, launched the Global Lighthouse Network in 2018 to identify manufacturers that are actively pushing toward the "fourth industrial revolution" by pursuing high efficiency, intelligence and green technologies.
A total of 22 manufacturing enterprises from ten countries joined the network in the recently released list of additions. Of these, 13 are Chinese factories, marking a historic high.
As of now, the total number of lighthouse factories worldwide has risen to 172, of which 74, or 43 percent of the total are from China.
Several of the additions are industry-firsts for the network, including the list's first nuclear power firm, the first coal mining machinery manufacturer, and the first rail transit equipment manufacturer.
Three of the 22 new additions are "sustainability lighthouses", each of which are Chinese enterprises.
Through the application of technologies such as artificial intelligence (AI) and the Internet of Things (IoT), as well as process innovations, these firms have reduced direct or indirect carbon emissions by over 20 percent, leading the world.
Generative AI, machine learning and other digital technologies were the key words in selecting this batch of lighthouses, according to the WEF, which estimated that the newly enlisted manufacturers have enhanced production efficiency by an average of 50 percent.
Central China's SANY Renewable Energy, a global provider of comprehensive wind power solutions, made the list after implementing swaths of AI and intelligent automation solutions on its factory floors.
Facility managers can monitor the real-time operation and the production parameters at various links through a small tablet PC.
"From the tablet computer, we can see the parameters of each production unit, from temperature and humidity to torque, and to the grinding fineness of the blades. All the data are provided to us in a comprehensive way to enable us to conduct real-time monitoring and delicacy management," said Peng Haibing, a manager of a SANY factory.
Wind turbine blades directly affect the performance and reliability of a wind power generation unit, whose cost accounts for 20 to 30 percent of the total cost of the unit.
The company has built a digital platform featuring the latest AI technologies to control the whole production process.
"This is a pioneering technology in our industry, which turns the 80,000-square-meter physical factory into a virtual one, with data about the overall structure and all the details of the factory. It is a benchmark technology in the wind turbine blade manufacturing sector," Peng said.
Through robots and laser-guiding technologies, the factory has achieved automatic operation at various links, including the grinding of blade surfaces, painting, and materials distribution. This has reduced the product defect rate by 20 percent and shortened the delivery time by over 30 percent.
Since the Global Lighthouse Network was launched, it has released 12 waves of additions. China has often topped the list and has seen at least two of its manufacturers added in each wave.
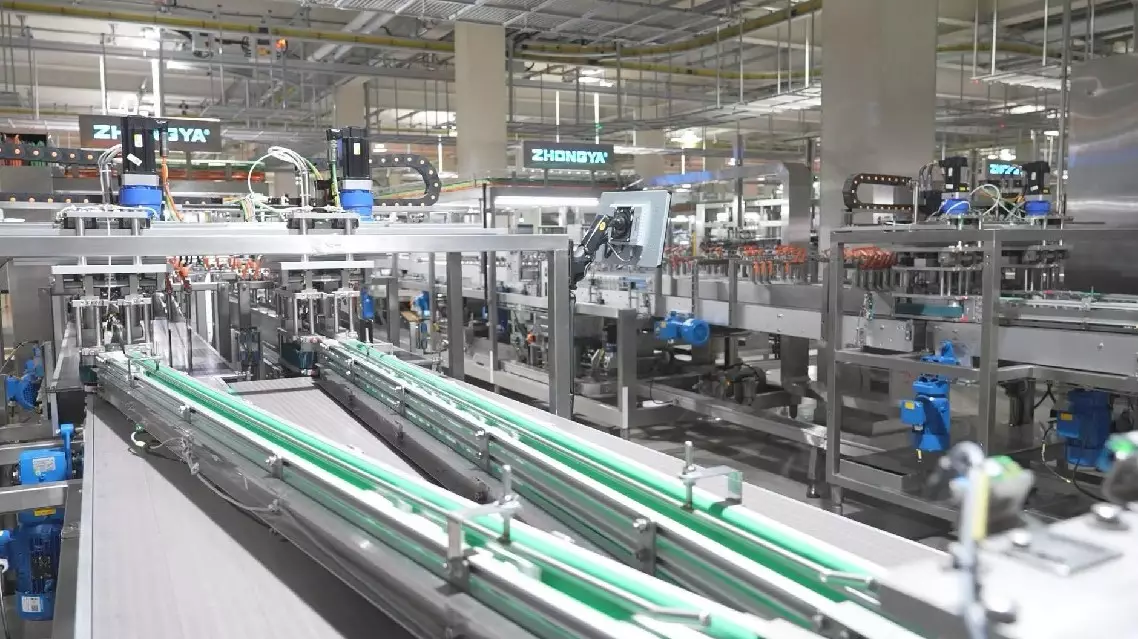
China claims most spots on World Economic Forum's latest "lighthouse" manufacturers list