An innovative, China-developed intelligent caisson robot has played a crucial role in completing the main structure of the Changtai Yangtze River Bridge in east China's Jiangsu Province, with its key ability to see in muddy water allowing more real-time monitoring and flexible drilling.
This advanced technology has significantly shortened the time required to construct the underwater foundation work needed for this project, which is designed to become the world's largest span cable-stayed bridge.
Due to the bridge's unique construction requirements, traditional drilling methods were inadequate for meeting the load-bearing demands of the main tower. The bridge's foundation differs from conventional suspension bridges; its main tower caissons are located within the river.
Employing cylindrical caissons, each weighing 23,000 tons, more than three times the weight of the Eiffel Tower, and covering an area equivalent to 13 basketball courts, these underwater caissons represent the world's largest underwater foundation.
Measuring 5.9 meters in length and 3.6 meters in height, the intelligent caisson robot, designed as China's first of its kind, operates underwater like a small truck. This pioneering robot ensures stability in anchoring even the most enormous underwater caissons.
To achieve uniform soil extraction in underwater visualization so that the giant caisson can take root smoothly in the water, the engineering construction team spent two years developing this smart caisson robotics system.
"This robot has realized one of its biggest difference-making functions: its ability to see underwater. With sonar and high-definition cameras for deep and muddy water, it operates underwater with real-time visual monitoring and adjustment," said Yang Le, director of large equipment department under China Railway Major Bridge Engineering Bureau Group Co., Ltd., responsible for the project construction.
Once deployed, the operator can adjust the robot's position using built-in range-finders and monitoring devices to its best working status.
"The drill in front has two functions: crush and absorb. By rotating the drill, the soil of various kinds is crushed and carried away by pipelines. Above the drill head is an 18-mega-pascal high-pressure water jet, which can break through hard soil layers and extract debris before suction. We also have a 380-cubic-meter-per-hour suction pump to remove sediment at an operation rate of 200 cubic meters per hour," Yang said.
The robotic arm's 360-degree mobility ensures even sediment extraction, which is critical for stabilizing the 300-meter caissons.
The robot also revolutionized underwater sediment removal, addressing risks of uneven excavation and tilt in traditional open caisson construction using air suction machines, which were also labor-intensive.
"In the past, soil extraction during caisson construction relied on vertical conduits and air suction methods. We could only rely on our experience, and such traditional ways are prone to uneven excavation and tilt of caissons," said Yang.
With the help of intelligent caisson robots, the construction team completed excavating and sinking the main tower caissons for the bridge two months ahead of schedule, ensuring that the main tower is more stable and securely anchored.
"Previous regular mud suction equipment required six workers per shift to move 40 cubic meters of sediment hourly. This robot only takes one man to operate in the operation room to increase the mud suction amount to 200 cubic meters per hour. That is four to six times faster," Yang said.
The Changtai Yangtze River Bridge is expected to open to traffic this year, reducing travel time between Changzhou and Taizhou to just 20 minutes.
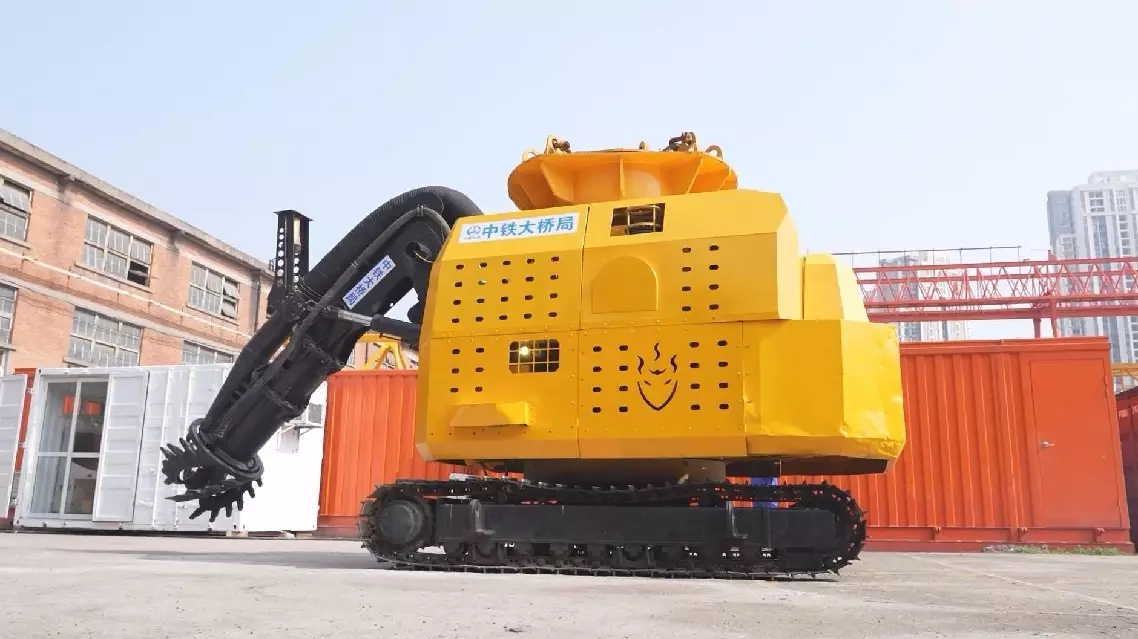
China-developed robot helps construct giant bridge in muddy water
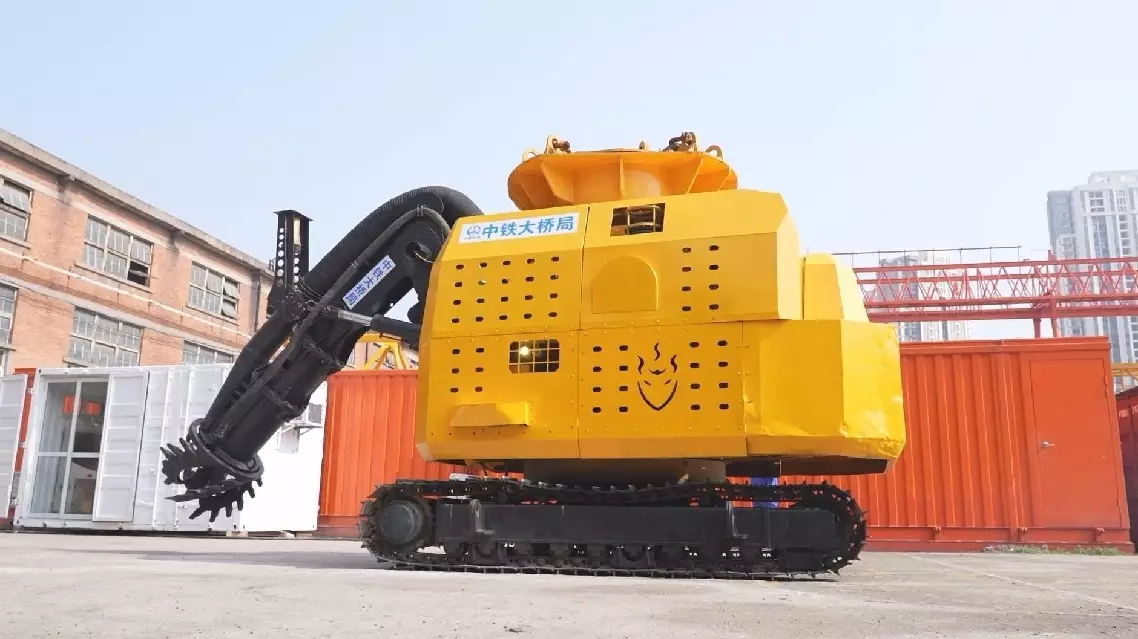
China-developed robot helps construct giant bridge in muddy water