內地科技巨頭小米首款電動車「SU7」早前上市後熱銷,其位於北京的新能源汽車超級工廠隨之揭密。
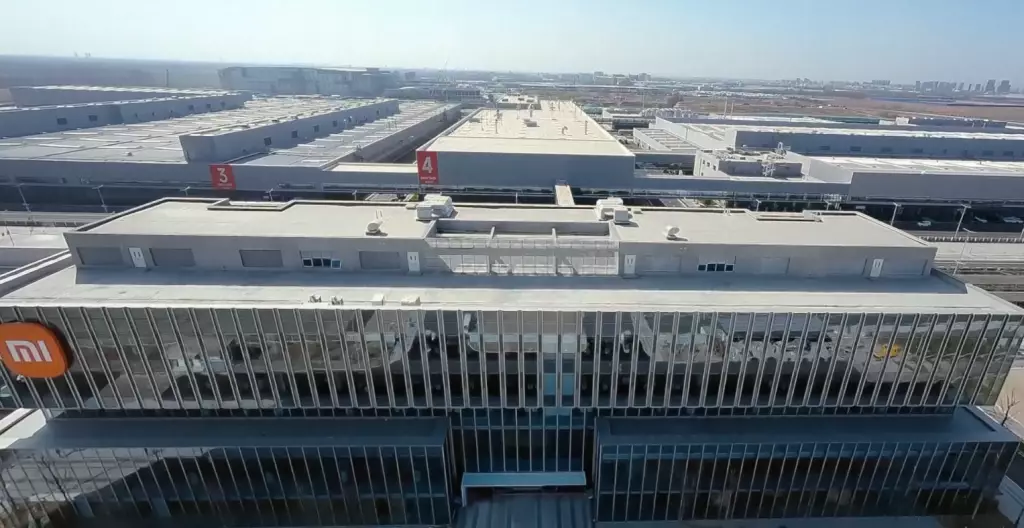
影片截圖
76秒就能產出一輛車 工廠規模堪比故宮
4月3日,小米SU7首批新車在小米汽車工廠正式交付,開售僅幾天就有逾10萬輛車的訂單,部分訂單交車時間已經排到半年後,小米位於北京的新能源汽車超級工廠亦隨之揭秘。據內媒報道,坐落於北京亦莊的小米汽車工廠具備高度自動化、智能化的特點,產能跑滿後,每76秒就能產出小米SU7,超過700個機器人直接服務於生產線,以提高生產效率和精度。

影片截圖
小米於2021年進軍新能源汽車領域,工廠佔地超過70萬平方米,相當於一個故宮的大小,工廠擁有壓鑄、衝壓、車身、塗裝、電池和總裝6大車間,並在這6個車間部署了700多台機器人,實現了汽車關鍵生產流程的全自動化,是目前全球最為先進的新能源汽車工廠之一。
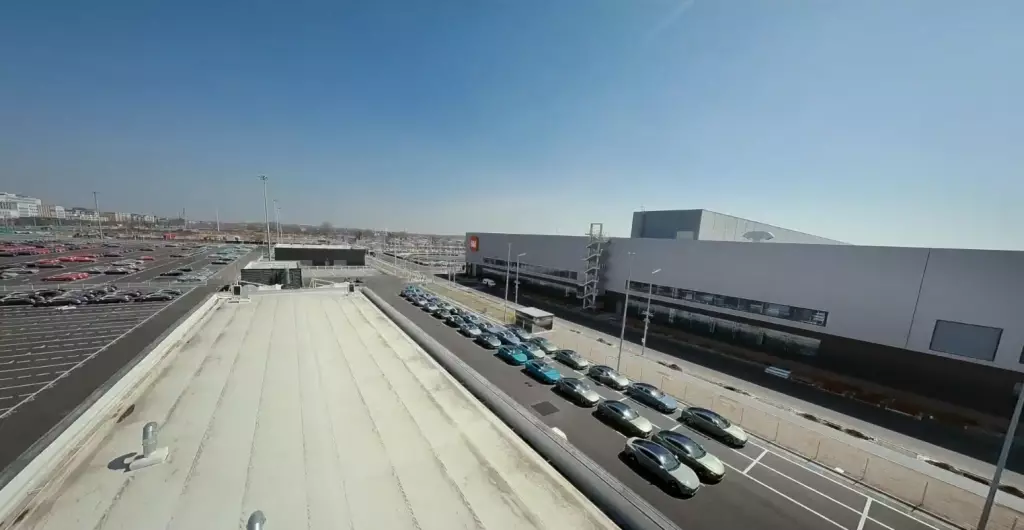
影片截圖
一體化大壓鑄集群 生產效率提升近10倍
在壓鑄車間,一台先進的大型機器可以一次完成新能源汽車後地板的壓鑄。過去,後地板的製造需要焊接 72 個零件,而機器的部署意味著減少了 840 個焊接點,生產效率提高了近十倍。另一個亮點是沖壓車間,該車間生產汽車的外部部件,包括門和麵板。
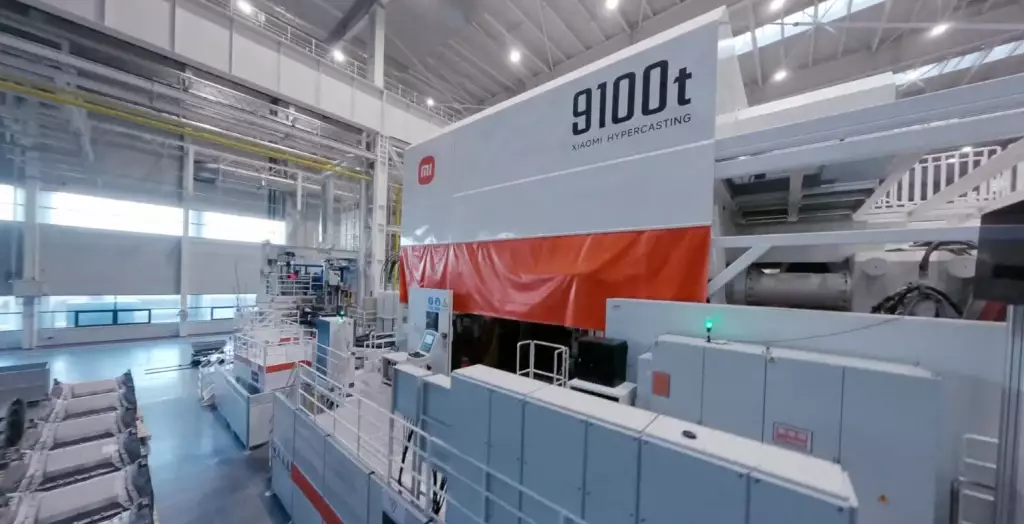
影片截圖
一套外部零件僅需4秒即可完成 速度快精度高
衝壓車間負責製作車的四門兩蓋、側圍外板等所有的車身外覆蓋件,生產一組零件平均僅需4秒。壓機線總噸位達到6900噸,可實現鋼板和鋁板的混線生產,處於業內頂級水準。此外,衝壓機的內部有六點式拉伸墊設計,相較於傳統的四點式衝壓,大大提高了精度,公差僅為發絲直徑的1/6,比普通模具研合精度提高了1倍以上。
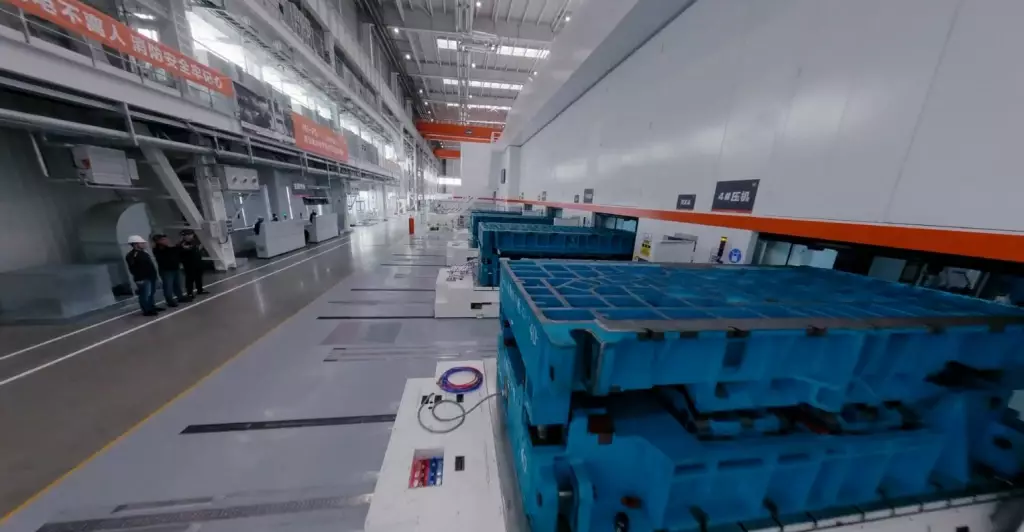
影片截圖
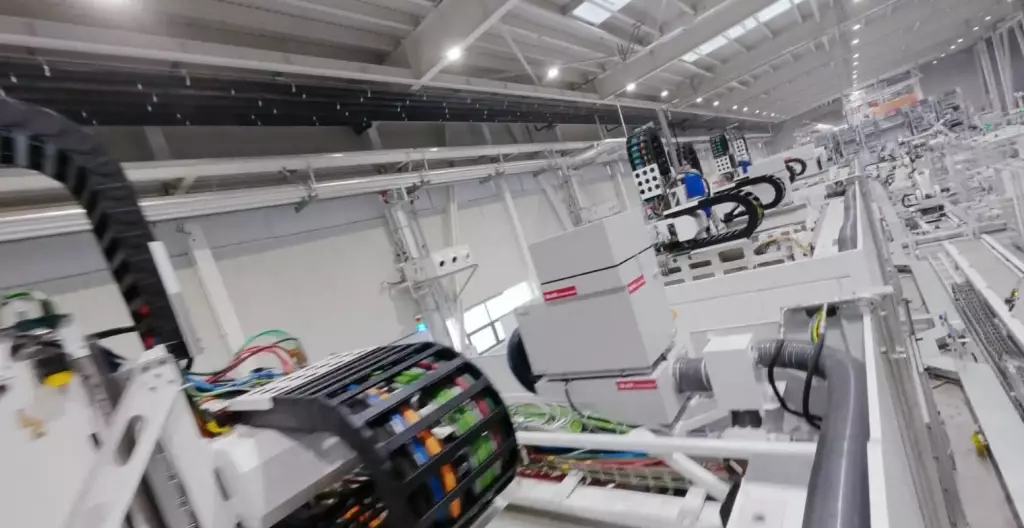
影片截圖
逾700機器人服務生產線 實現關鍵工藝全自動化
在整個工廠,超過700個機器人服務了生產線的全過程。車身外覆蓋件100%實現了自動裝調。2340個工藝連接點同樣也是100%由機器人完成作業。從拼裝連接到線上檢測,工廠實現了關鍵工藝100%自動化。
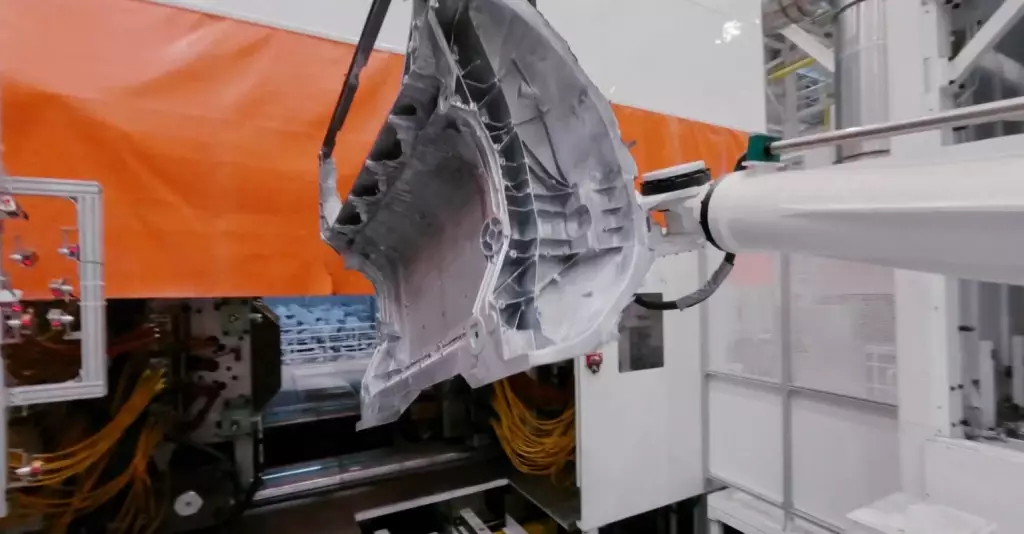
影片截圖
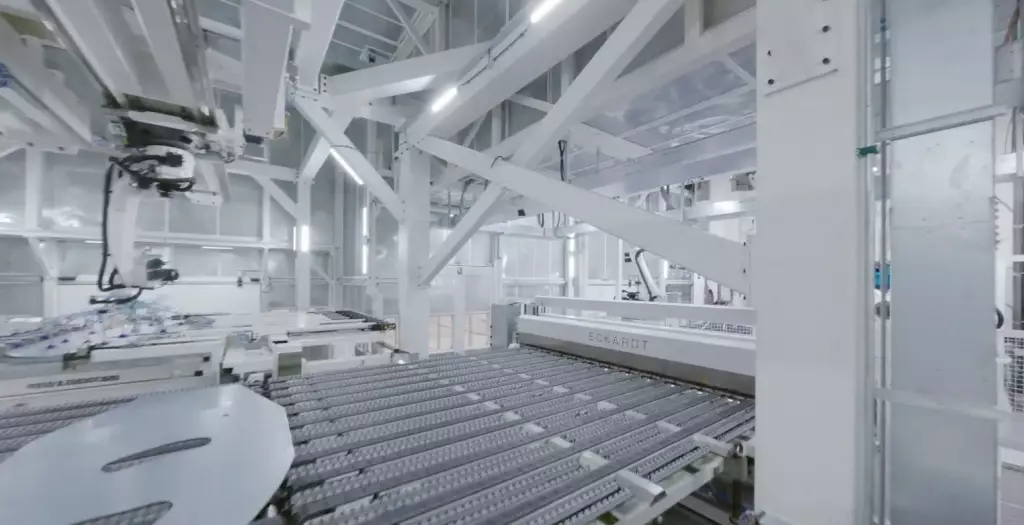
影片截圖
AI統一調度 靈活調整路線
車身車間是整個工廠機器人使用程度最高、自動化率最高的一個車間。採用最新一代AMR物流機器人,完全依靠AI演算法實現運輸,完全擺脫了之前需要在地面設置磁線進行引導,它可以根據各個車間的生產實際情況,去靈活自主地調整路線。
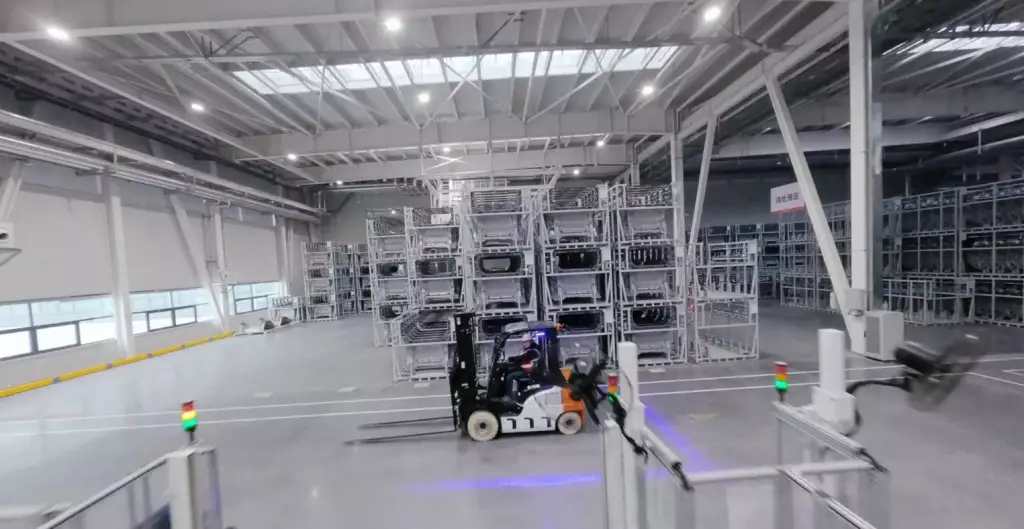
影片截圖